Core Technologies
VIRC has obtained 5 system certifications and 5 product certifications, holding over 50 patents related to starting power sources. Our 20+ core technologies include: “CTB Technology, Ultra-High Power Technology, Full Tab Stacking Technology, Flame Retardant Technology, Integrated Design, Intelligent Management System, Anti-Corrosion Technology, Automotive-Grade Explosion-Proof Technology, High-Frequency Sealing Technology, and Anti-Theft Security Technology, etc.
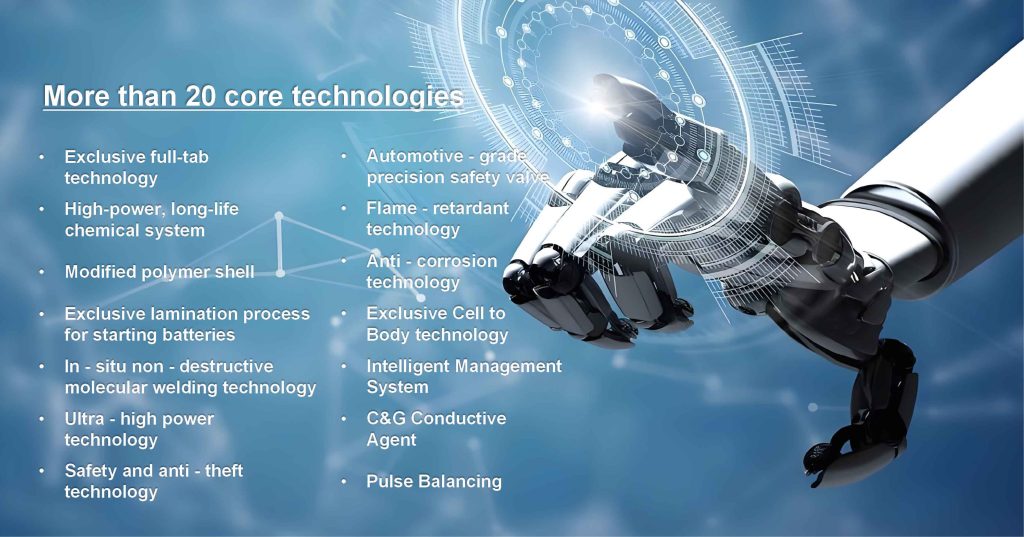
High-Power Long-Life Chemical System
Long - Life Chemical System
Carbon Coating
Enhanced conductivity through carbon introduction (coating/doping) reduces battery impedance by 15-25%, improving power density and cycle performance.
Nanonization Technology
Optimize the particle size and morphology of materials, prepare nanomaterials, shorten the solid-phase diffusion path of lithium ions, and enhance the lithium-ion diffusion ability. These measures can improve the power performance of lithium-ion batteries.
Flame - Retardant Technology
Flame - Retardant Electrolyte
Under thermal runaway conditions, the release of free radical scavengers interrupts the chain combustion reactions, thereby preventing the internal spread of thermal runaway.
Flame - Retardant Separator
Our self – developed, environmentally friendly halogen – free flame – retardant separator forms a heat – insulating and oxygen – blocking protective layer on its surface during thermal runaway. Meanwhile, it releases non – flammable gases, reducing the risk of thermal runaway in the battery cells.
Heteropolar Full-Tab Structure
High - Power
Innovative full-tab design enables loss-free current collector extraction from both ends of the cell, forming a lossless full-tab structure. This significantly increases current pathways, elevating output power by 5-10x.
Extended Lifespan
Dual-terminal tab configuration combined with full-tab architecture reduces resistance, mitigates heat generation and accumulation risks, and enhances electrode consistency. This extends battery lifespan by 3-5x.
Simplified Manufacturing
Streamlines die-cutting processes, improving production efficiency while reducing defect rates by 17% to ensure product quality.
Exclusive Stacking Technology
Superior Energy Density
Structurally Safe & Stable
Eliminates uneven internal stress from winding corners. Uniform expansion forces across layers during charge/discharge ensure structural integrity, minimizing risks of bulging, short circuits, or fractures.
Enhanced Performance
The number of tabs is double that of wound batteries, optimizing the electron transfer path and reducing the internal resistance by over 10%. This results in less charge – discharge polarization, less heat generation, lower energy consumption, and fewer side reactions, making it more suitable for high – rate and long – life applications.
Exclusive CTB (Cell-to-Battery) Technology
Innovation in Cell Manufacturing Processes
CTB technology eliminates 24 process steps, boosting cell consistency by 70% while optimizing production workflows and product quality.
Optimized Pack System
By leveraging the CellToBattery technology, the Battery Management System (BMS) accomplishes end – to – end wireless harness management. This not only cuts down on energy consumption losses and failure rates but also enhances the precision of current and voltage sampling management.
Cost Reduction and Efficiency Improvement
Utilizing CellToBattery technology, the elimination of Pack assembly streamlines processes, reduces facility footprint and labor costs, while saving on material expenses for Pack interconnects.
Modified Polymer Enclosure
Uncompromised Safety
Using a modified polymer shell, compared with conventional batteries, it has an extremely low deformation rate (≤1%), completely eliminating potential safety hazards such as swelling and explosion.
Corrosion Prevention And Heat Insulation
Melting point (~160°C, vs. 660°C for aluminum or 1500°C for steel) enables rapid pressure relief during thermal events, improving safety by 75%.
Precision Safety Valve
Complementary Material Properties
Synergistic Sealing
Aluminum-fluoroelastomer integration creates a complementary synergy, maintaining internal pressure equilibrium under extreme vibration, impact, or thermal shock for dual-layer protection.
Precise Burst Pressure
Tailored burst pressure settings adapt to diverse environments (e.g., high-altitude, high-humidity), delivering scenario-specific safety. This multi-dimensional protection elevates battery safety by 100%, offering unprecedented security for users and equipment.